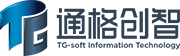
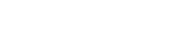
行業新聞 2025-05-07
在全球工業4.0浪潮的推動下,制造業正迎來一場“物理世界”與“數字世界”深度融合的革命性變革。對于年產值在5000萬至5億元的中小型制造企業來說,ERP系統的選型決策至關重要。它不僅關系到企業運營效率的提升,更是企業在數字化能力競賽中能否生存的關鍵。傳統ERP系統以財務核算為核心的設計邏輯,與制造業以“車間為中心”的運營需求存在結構性矛盾。而DELMIAWORKS作為達索系統旗下專注于制造業的ERP解決方案,憑借其“生于車間、長于制造”的獨特基因,正在為中小企業搭建起數字化轉型的黃金通道
傳統ERP的三大致命短板與選型困境
傳統ERP系統脫胎于20世紀60年代的物料需求計劃(MRP),其底層架構圍繞財務核算和供應鏈優化展開。這種設計導致車間動態數據(如設備參數、工藝波動)被簡化為靜態工單數據,形成"財務數據精準但生產執行失控"的典型悖論。例如某沖壓企業發現,傳統ERP記錄的模具使用次數與實際損耗成本偏差高達35%。
離散制造企業常需處理復雜工藝路線(如熱處理、精密加工),但傳統ERP與MES(制造執行系統)的分離架構迫使企業投入高昂的集成成本。調查顯示,67%的中小企業因預算限制被迫使用"Excel排產+人工調度"的原始模式,導致訂單交付準時率普遍低于75%。
傳統ERP的財務導向導致數據顆粒度難以支撐制造優化。某CNC加工中心發現,其設備能耗成本按固定比例分攤的方式,掩蓋了主軸磨損導致的電費異常(實際偏差達28%)。這種粗放式核算使企業錯失工藝優化機會。
DELMIAWORKS的破局之道:
車間驅動的操作系統
DELMIAWORKS顛覆傳統ERP的設計原點,構建以車間運營為中樞的數字化平臺。其突破性體現在:
●
動態制造BOM管理:支持工藝參數與設備能力的關聯。當汽車零部件熱處理溫度需調整時,系統更新工藝路線并同步成本模型
●
實時排程引擎:內置APS模塊整合設備稼動率、物料庫存等實時數據,幫助企業將排產效率提升40%,訂單交付準時率躍升至95%
●
全流程質量追溯:滿足汽車零配件IATF16949與醫療器械行業ISO13485合規性要求
通過原生融合ERP與MES功能,DELMIAWORKS構建起覆蓋"訂單-計劃-生產-交付"的閉環體系:
●
工單級數據顆粒度:支持按工序/設備/班組維度核算成本,浙江某五金廠借此發現某沖壓工序模具損耗占比達15%,經優化后單件成本下降12%
●
預測性決策支持:預警供應鏈波動,生成替代采購方案,某電子代工廠庫存周轉率提升30%
●
全球化協同平臺:多工廠數據看板實現全球產能調度,某工業設備廠商海外庫存周轉率提升30%
破解選型難題的DELMIAWORKS方案
DELMIAWORKS通過28種工藝模板(沖壓/焊接/熱處理等)實現工業場景的精準刻畫。在熱處理工序中,系統可自動關聯烤箱容量、溫控曲線等參數,實現工藝條件與生產指令的智能匹配。
采用"可擴展平臺"設計平衡標準化與定制化:
●
36個預配置模塊:覆蓋ERP/MES/WMS/CRM核心領域
●
可視化排產工具:甘特圖拖拽式操作降低技術改造門檻
●
按需擴展模式:支持從基礎PMC模塊到全鏈條數字化升級
通過單一數據庫實現業務流、生產流、財務流的三維融合:
●
實時計劃運營(Real Time PMC):整合車間數據提升排產準確率40%
●
穿透式質量管理:構建全生命周期質量檔案,減少廢品損失15%-20%
●
業財無縫對接:車間報工數據自動觸發核算,財務周期縮短70%
實踐驗證:數字化轉型黃金路徑
●
實施周期壓縮:核心模塊3個月上線,較傳統ERP縮短50%
●
生產效率飛躍:APS智能排產提升設備利用率至85%
●
管理可視化突破:車間看板實時監控OEE,異常響應縮至30分鐘
分步實施策略建議:
●
需求聚焦:優先解決生產瓶頸(如計劃排產/質量追溯)
●
漸進擴展:從PMC模塊切入,逐步延伸至供應鏈協同
●
生態協同:選擇具備制造經驗的本地服務商(如普華信息)
結語:重構制造業ERP的價值坐標
DELMIAWORKS的顛覆性創新在于將ERP從"記錄工具"進化為"制造操作系統"。對于中小企業而言,這不僅是用一套系統替代分散的ERP/MES/SCM,更是通過車間數據的實時流動構建"設計-制造-改進"的創新閉環。當設備振動頻率、操作員技能圖譜、物料周轉軌跡都能轉化為管理語言時,中小企業便真正獲得了與行業巨頭同臺競技的數字化杠桿。
在工業4.0的競技場上,DELMIAWORKS通過"低成本起步、高彈性生長"的數字化轉型路徑,正在重構ERP的選型邏輯——從被動"系統適配"轉向主動"業務賦能"。這種OT與IT的深度融合,讓中小型制造企業得以在變革浪潮中完成從"生存游戲"到"創新競賽"的驚險一躍。
通格創智是達索SOLIDWORKS大中華區核心經銷商和增值服務商,如有DELMIAWORKS采購需求可與我們聯系,服務熱線:400-112-8028
行業新聞
行業新聞
行業新聞
行業新聞
在線課程
行業新聞